
September
2006
TO MARK OR NOT TO MARK
Multi-channel visual display systems in simulation
& training theaters typically employ cylindrical,
conical or spherical curved projection screen surfaces
for display of the OTW graphics information. These
curved screens provide wide fields of view up to 360
degrees to create visually realistic training environments.
Older simulators have traditionally used CRT based
video projectors, while new systems and upgrades today
are typically using solid-state projectors with LCD/LCOS
or DLP based light engines. Being analog devices,
the CRT projectors have the ability to "warp"
the shape of the projected image to correct for geometric
distortions due to the curvature of the projection
screen. This 'warping" feature is, to a degree,
inherent in the design of the CRT projector. The newer
solid-state projectors do not have this "inherent"
warping capability and, therefore, typically use video
pre-processors to re-map the image geometry prior
to feeding the video signal to the projector(s). Some
projector manufacturers integrate this pre-processor
warping function circuitry into the projector housing,
however Display Solutions does not recommend this
configuration because it restricts the choice of available
projectors and has higher life cycle cost implications.
With
the CRT based projectors, it was necessary to "map"
the projection screen to define the correct geometric
shape of the resultant image. Once the screen was
mapped, the system installer then made manual adjustments
to the CRT projector to match a projected test pattern
to the screen map. The end result was a projected
image that was relatively distortion free on the curved
screen surface. To achieve reasonable geometric accuracy
over the entire image, higher end projectors typically
had the ability to control geometry (and convergence)
in 50 or more (almost) independent zones. While the
results were generally acceptable, it was a time consuming
procedure and required fairly regular maintenance
adjustment due to "drift" of the analog
circuits employed in the projector.
One
of the advantages of the new solid-state projectors
is that they are digital devices and essentially immune
to the "drifts" encountered in analog devices.
The video warping processors are also digital processors
and equally immune to electrical drift. The better
warping systems use "real-time" processors
allowing WYSIWYG adjustment of the warping parameters
while viewing the projected image. The geometry modifications
can then be made in much the same fashion as is done
with the CRT projectors i.e. mapping the screen and
then making manual adjustments via the warping processor.
One
of the problems with this method is, in fact, the
mapping of the screen. This mapping is usually performed
by using a laser theodolite located at the "eye
point" or center of curvature of the theater.
Radial points are then identified, usually corresponding
to an available test image that is projected onto
the screen. The screen is then "marked"
at these points and the markers are used to correlate
the test image to the proper locations on the screen.
This, of course, assumes that all points on the screen
are easily reachable. In domes or with screens with
high height dimensions, this is not always the case.
In order to avoid having the markers visibly interfere
with the actual images during normal training sessions,
an ultraviolet ink is generally used for marking the
screen. The screen is illuminated with a UV light
source during installation and/or maintenance, rendering
the markers visible for adjustment purposes. The markers
are not visible when the screen is illuminated with
the projection light source only. Another method of
"marking" the screen is to drill tiny holes
thru the screen at the locations identified by the
laser theodolite and inserting small LED's into the
screen. The LED's are illuminated during the "set-up"
process providing a visible marker pattern for alignment.
When the LED's are turned off, they are essentially
invisible to the viewer during training.
These
methods of mapping the screen are somewhat time consuming,
but, again, they also depend on having "line-of-sight"
access to all points on the screen from the "eye-point".
In marine simulators, this is often not the case due
to the size of the ship bridge structure. Laser levels
can also be used to create a geometric map on the
screen surface and are often used in addition to other
screen markings to facilitate the alignment process.
However, once the alignment is complete and the lasers
removed, there is no marker pattern remaining for
future maintenance purposes (e.g. replacing failed
projectors). Permanent laser diode arrays are sometimes
employed (at substantial cost) to create a marker
array that can be turned on as needed. It is an acceptable
solution provided there are no "line-of-sight"
issues between the theodolite and the eye-point preventing
complete marking of the screen.
An
alternate method used by Display Solutions in many
of our installations utilizes an "automated"
geometry alignment process. This feature is offered
as part of the toolset in the 3D Perception CompactDesigner
user interface (GUI) SW associated with their CompactUTM
series of video warping processors. CompactDesigner
includes a low level solid modeling CAD package for
theater design. The CompactDesigner tool set is used
to design the complete theater visual system layout,
including obstructions (e.g. bridge house, beams,
etc), projectors and screen(s). The CAD package includes
capabilities to model specific projectors to account
for projector size/location, lens characteristics,
projector orientation and lens shift. Once the visual
system is modeled in the CAD solids package, the SW
calculates the geometry distortions required to correct
for screen shape and projection angles and downloads
the correction factors directly into the warping processor
HW. Provision is made in the SW to input the image
generator parameters such as resolution, VFOV, HFOV,
etc directly into the CAD layout. These parameters
are accounted for in calculating the distortion coefficients
to be downloaded into the warper boards. The CAD model
is developed as part of the initial design process
and used to establish feasibility and guide the physical
installation of the visual system components. After
the installation is completed, the model is updated
to "as-built" to reflect any deviations
required by the physical environment. The resulting
image pattern projected onto the screen surface contains
the equivalent accuracy of a manual alignment using
hundreds of "control points" in the warping
pattern. Typically, a minimal amount of final touchup
geometry adjustment is required for optimum registration
between channels in the edge blend zone of the composite
image. The need to do anything but basic screen marking
(e.g. channel ctr positions which can be marked "off-screen")
is essentially eliminated with this procedure. Both
geometric accuracy and speed of setup are superior
to manual alignment and screen mapping procedures.
Display
Solutions, in close cooperation with 3-D Perception,
has pioneered this method to improve installation
quality, speed and ease of maintenance for theses
systems. Display Solutions uses all of the methods
discussed for various installations, depending on
the demands of the specific design and customer preferences.
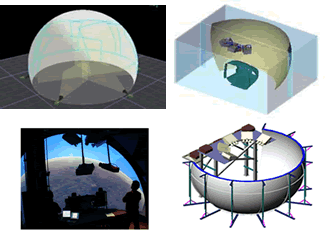
|